1) Production of wax patterns
The prepared fluid wax mixture is injected into duraluminum molds of our own production.
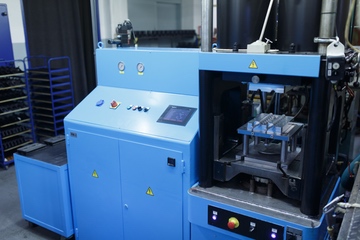
2) Assembly of wax patterns to a tree
Wax patterns are assembled and attached to the sprue gate system (creating a so-called “casting tree”).
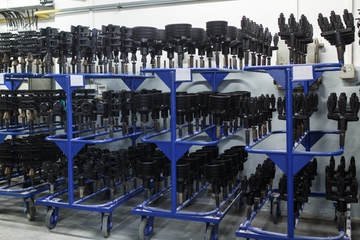
3) Coating of wax patterns with ceramic slurry and sand
Each casting tree is dipped in ceramic slurry based on SiO2 and siliceous sand and then dried in air-conditioned premises.
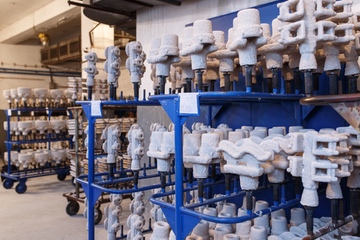
4) De-waxing in autoclave and shell firing
The wax is melted off the shell in autoclave using hot steam. The shells are fired 980°C just before the casting.
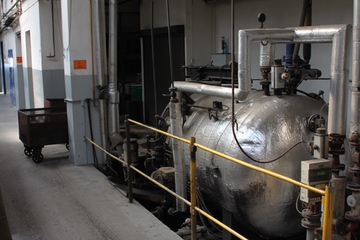
5) Casting
The metal is melted in medium frequency furnaces with thyristor converter (200 kW, capacity 2 x 100 kg).
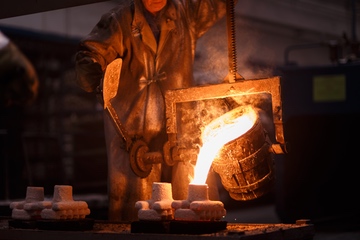
6) Removal of ceramics
The ceramic shell is removed from the cooled castings in a vibrating machine.
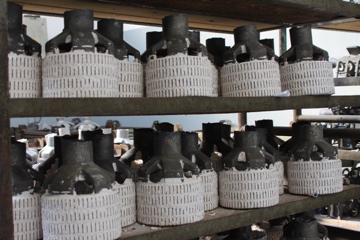
7) Finishing operations
The castings are being finished and undergo the final treatment.
- Pre-blasting in a chamber blaster
- Cutting machines cut off the castings
- Heat treatment
- Final abrasive blasting (per steel type)
- Machining, grinding, polishing and surface finishing
8) Visual and dimension inspection
There is a full visual inspection of each casting. Dimensional inspection of wax patterns and the final castings (3D measuring possible takes place. The whole process of casting production is monitored and controlled by an independent inspection.
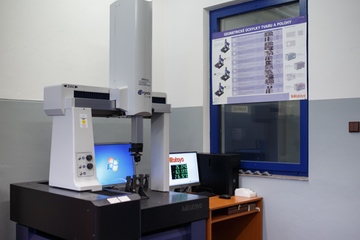
9) Packaging and shipping
The final casting is packaged according to the customers’ specification and delivered in a timely manner.
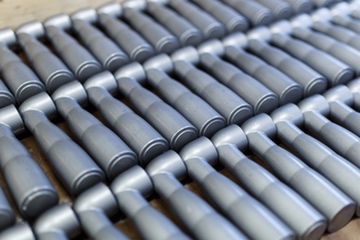